
Boosting Warehouse Accuracy and Speed with TIM’s Integrated Solutions
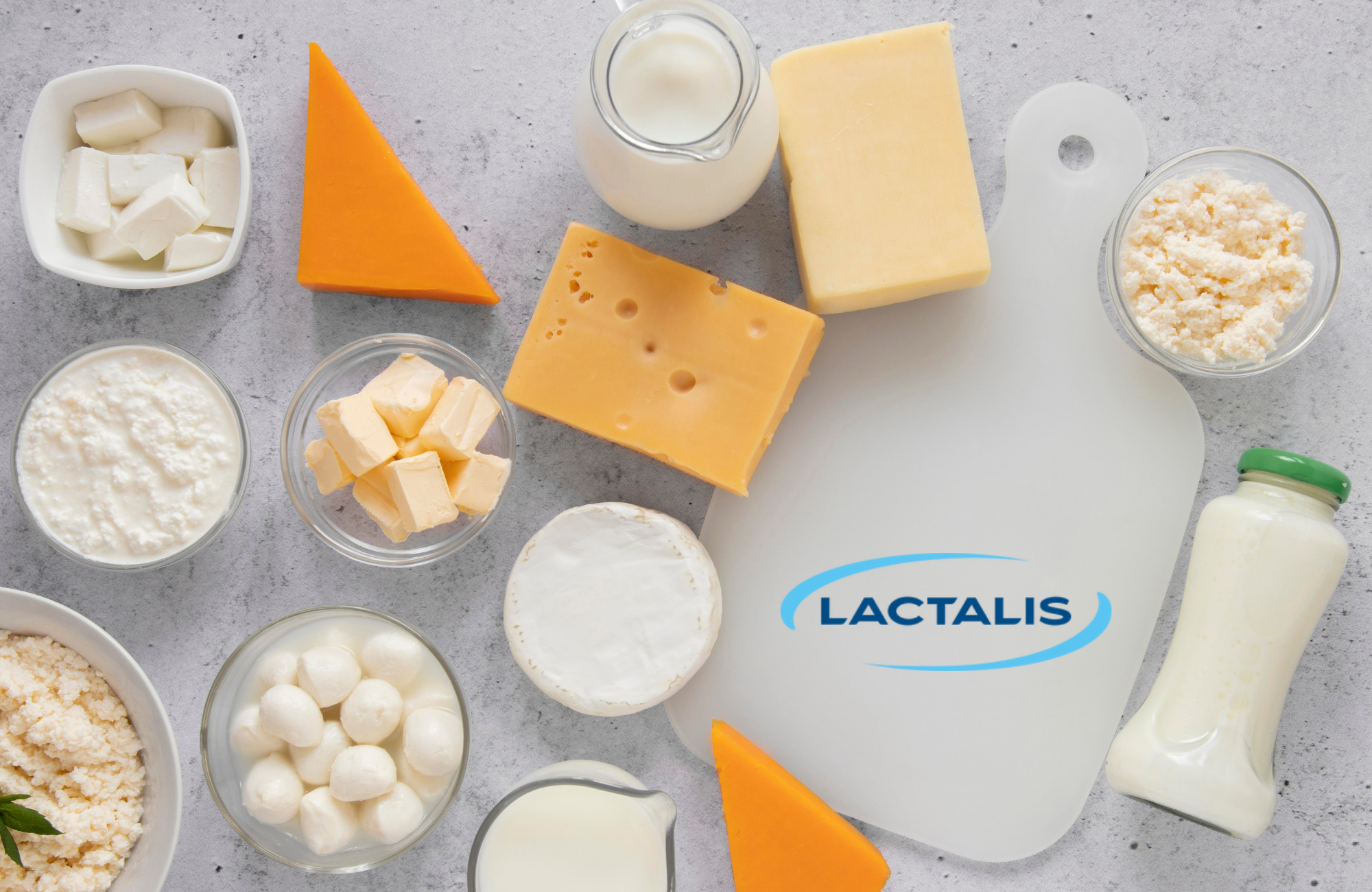
Industry
Manufacturing
Challenge
Lactalis was facing inefficiencies in its warehouse operations due to manual pallet picking and tracking processes. These challenges led to avoidable errors, slower workflows, and increased operational costs, creating the need for a more reliable and scalable solution.
Results
With TIM’s integrated solutions, Lactalis significantly improved the accuracy and speed of its warehouse processes. Real-time guidance, automated tracking, and seamless order management reduced error rates and streamlined operations across the board.
Product Used
Vega - X
The Challenge
Lactalis’ warehouse operations involved manual pallet picking, which often led to operational disruptions, incorrect shipments, and increased costs. Error rates in product picking ranged between 3% and 5%, causing inefficiencies and potential customer dissatisfaction—particularly for a large-scale manufacturing operation.
The Solution
To resolve these issues, Lactalis implemented Thread in Motion’s integrated wearable technology. TIM’s solution, combining smart interfaces with Vega-X and Axata system integration, enabled real-time order management and barcode tracking. Warehouse staff received immediate visual instructions on their wearable screens, allowing them to follow the correct picking sequence and significantly reduce the risk of error.
The Results
The technology enhanced product tracking accuracy and streamlined the picking process. Each order was displayed in real time, and barcode scanning ensured correct product selection. This resulted in minimized manual errors, accelerated order processing, and stronger logistics performance across Lactalis’ warehouse operations.
Read the full success story and see how innovation drives results!